Self / Remote Operating Equipment in Mining
Our Keelan Mooney writes in a series of blog posts exploring how mining will play its part in the race for a carbon-neutral world. He will look at how mining is changing and the challenges for both the mining sector and the insurance world. In this fourth chapter, Keelan will explore remote operating or autonomous systems in mining.
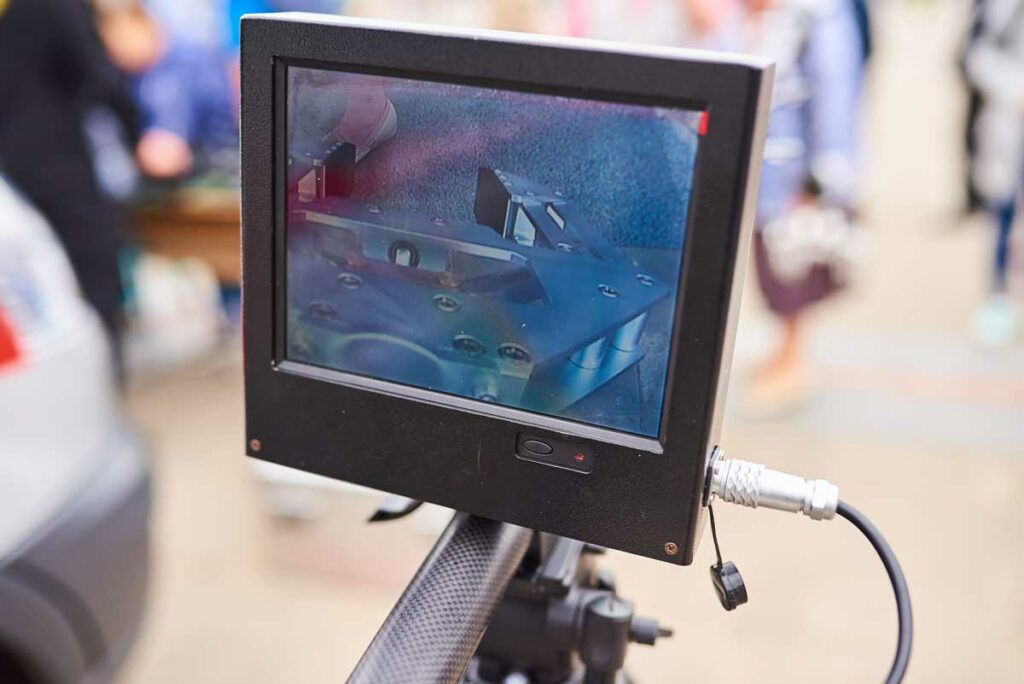
One way of handling risk is eliminating the source. However, is that the best solution when it comes to operating large mining equipment?
Mining equipment such as Autonomous Haul Systems (AHS) and underground bolters have the technology to be self or remote operated. In fact, AHS are already deployed in mines across the globe and have been for some time, including a recent uptick in Canadian operations.
Insurers would have to consider how the risk and liability of the automated vehicles would be addressed. It has been observed that autonomous trucks will follow an identical path of travel every trip, however when road conditions deteriorate and require repairs how will the AHS respond? Unidentified this could lead to a road/berm failure or accident. Capital costs can increase when using AHS systems and require new networking and infrastructure to support the GPS guidance and data collection, which could impact the quantum of a property damage loss as well as potentially increasing business interruption losses from the increase in productivity produced by AHS.
It is widely viewed that the advantages of and AHS system out way the disadvantages. Advantages include:
- A self-operating fleet can reduce labour costs and reduced maintenance,
- Narrower margins permitted in mine designs,
- Increased salaries to encourage skilled workers from saving produced in operations,
- Improved safety removing personnel from dangerous situations,
- Better economics can lead to opening closed or currently unfeasible mines increasing supply to the market and producing jobs from an increase in operations.
Converting to a new fleet does not happen overnight and there are constraints to the success such as:
- Timing can play a part in the conversion of a standard fleet to a remote or self-operating fleet. It may be a better use of capital for operators to update their fleet at the time the old fleet has reached the end of its life.
- Various levels of automation required. i.e fully versus partially.
- Depends on mine layout and constraints, open pit vs underground.
With huge advancements in the recent decade, AHS systems are still being adopted into the industry and scepticism is still prevalent around the proven technology. This is a challenge for the industry as it continues to attempt to improve its safety records and test the limits of mine designs to improve the feasibility of new mines.
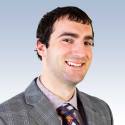
Keelan Mooney, EIT | Loss Adjuster
If you enjoyed this article and want to keep up to date with future chapters, please submit your email address below.
[mc4wp_form id=”20520″]
Please note: Submitting your email address subscribes you to this blog series only. You can unsubscribe at any time via the link in the email.