Oil and gas maintenance managers voice procedure and equipment concerns
A new study reveals that unnecessary growth in the number of processes and procedures and lack of equipment reliability are the biggest concerns for maintenance managers in the oil and gas industry.
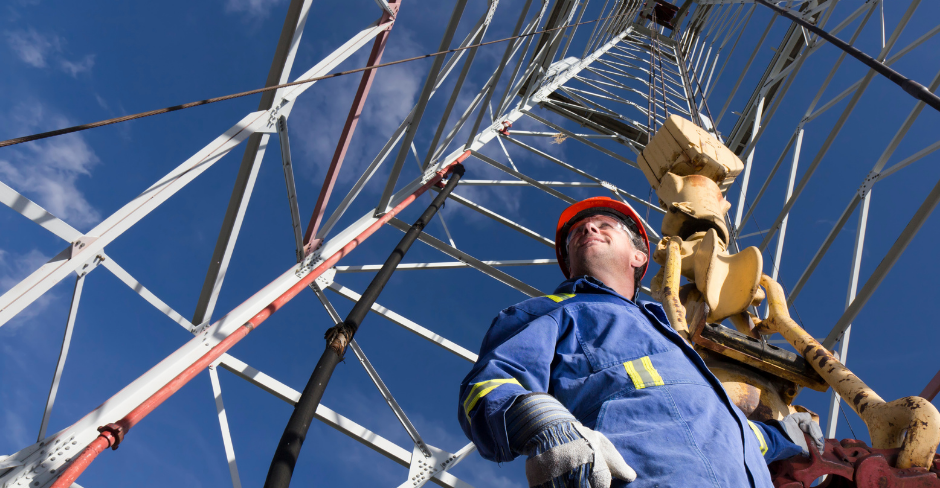
The survey, conducted by asset integrity management specialist Add Energy, was completed by more than 400 maintenance managers worldwide, from large multinational companies to smaller regional businesses. Add Energy’s team of maintenance experts have analyzed the data and provided insights and recommendations based on their experience.
“The purpose of the study is to enable maintenance managers to utilize its findings and conclusions to develop approaches and solutions for common maintenance challenges,” says Peter Adam, EVP of Asset and Integrity Management at Add Energy.
Process and procedure pains
The oil and gas industry has in recent years invested heavily in the simplification of work processes in order to bring down both capex investments and operating expenditure. Despite this, 58 percent of maintenance managers claim that the growing volume of processes and procedures is more challenging now than it was five years ago.
While a growing volume of processes and procedures are being created, the rate of adoption is not following the same pace. This is seen to decrease tool time (42 percent of respondents), places an unnecessary burden on skilled technicians, and takes away decision making from competent team members.
“More processes and procedures are created in the belief that they are the solution for skills and competency gaps. However, most of the time this documentation is created by back office staff who do not rely on the insight of their field colleagues as much they should. Instead of masking issues with processes and procedures, the oil and gas industry should be focusing on valuable training instead of the tick-the-box style of training. This will enhance competence and eliminate skills gaps, which in turn means that we can trust people to do their jobs correctly, efficiently and safely,” says Peter Adam.
Equipment reliability
In the survey, 40 percent of maintenance managers state that reliability of equipment is the biggest challenge they face today.
“More and more equipment is working beyond its original design life. Coupled with the past years’ decline in maintenance budgets, it is not surprising to see widespread concern over equipment reliability levels,” adds Peter Adam.
Getting people to use the computerized maintenance management system (CMMS) is cited as the second biggest challenge, with 37 percent of respondents voicing their concerns over this.
“This indicates that either the initial implementation training was insufficient or that there has been an erosion of CMMS expertise post implementation. Either way, not capitalizing on such a sizeable investment is a certain way of ensuring that maintenance of oil and gas assets is less cost-efficient than it could have been,” adds Peter Adam.
Increased budgets
On the plus side, the survey shows that over 70 percent of maintenance managers believe that the majority of their work is planned. Further, approximately 50 percent of maintenance managers rate both their team and maintenance strategy as highly effective.
At the same time, 71 percent of the maintenance managers also say that planning and scheduling is what their teams struggle the most with.
Just above 56 percent of maintenance managers expect that their maintenance budget will increase next year, with 21 percent expecting a decrease. The majority (60 percent) will focus on improving facilities, plant and machinery next year.
If maintenance managers were given additional budgets, they say that they would spend it on upgrading systems (52 percent), hiring more people (44 percent) and upgrading or modifying current equipment (42 percent).
“The survey data clearly shows that there has been significant pressure on maintenance budgets. Upgrading and modifying systems and equipment are unsurprisingly high on the list as companies are being asked to sweat their assets harder and longer, requiring replacement parts that may not be in production anymore, along with increasing degradation and obsolescence,” says Peter Adam.
Add Energy is a subsidiary of Oslo-listed energy consultancy group ABL Group ASA. The company offers solutions and specialized consultancy services to the energy industry, plus training of personnel and a unique toolbox of proprietary software and analytical tools.