JH143 Shipyard Risk Assessments: An inside look by veteran surveyor Matthias Wittek
The JH143 Shipyard risk assessment process was developed originally by ABL in 2003 in coordination with Joint Hull Committee. The aim of the risk assessment is to assess risks at a shipyard or on a running vessel allowing underwriters to consider their exposure and mitigate the risks where possible.
We interviewed our expert on the matter, Matthias Wittek, Naval Architect for ABL, based in Hamburg, who assisted in the process of creating the standard and has been performing JH143 risk assessments ever since.
ABL Surveyors are highly experienced on working on both shipyard surveys, encompassing all ongoing projects in the shipyard, or individual project surveys for a specific vessel, either newbuild or undergoing repairs.
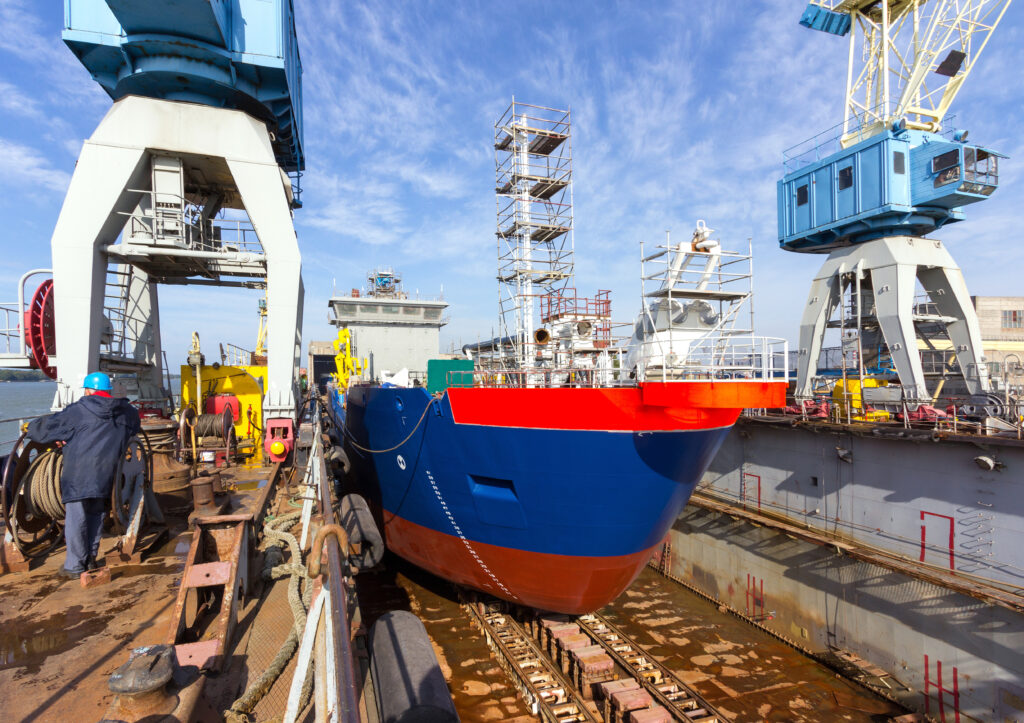
Matthias, how long have you been doing JH143 surveys and how many do you think you have done?
I’ve been doing JH143 surveys since they were formally established by the Joint Hull Committee in 2003 with the assistance of our company. I used to do the JH143 surveys (both project specific and shipyard surveys) in parallel to my activities as a surveyor for hull and machinery claims but now I’m doing nearly only JH143 surveys.
As for the number, it will be several hundred surveys since then. During this year alone, I have worked on 21 different shipyards with corresponding projects or newbuilds plus several supervisions for colleague surveys. Our engagement for a newbuild or project can vary from a single attendance to 4 or more per year.
Where have you travelled for JH143 surveys?
Literally all around the world, in Europe I’ve been to Germany, Poland, Denmark, Sweden, Norway, Finland, Italy, Croatia, Spain, Estonia and Northern Ireland. In the Middle East I’ve been to the UAE; I’ve also been to South Africa and Brazil and Canada.
Realistically, do you think it is possible for a shipyard to receive a Grade A in JH143?
It is possible but only on a long-term audit process. This process takes a while as the shipyard must implement all recommended instructions into their own manuals and procedures, create a specific Safety Concept for each project vessel or newbuilt and should be already 2 years under our audit regime. To answer the question, I’ve given a Grade A on my first shipyard survey in 2003, but this was based on a not yet defined company grading standard.
What is the most common risk you see in a shipyard?
The most common risk is that of fire as if it comes out of control it can destroy the entire project. Well prepared shipyards have their own fire squad team or firebrigade and can be on site for the emergency in 5 minutes or less. Based on our experience it should be noted that if a shipyard is not able to response to a fire and contain it in time with its own resources but needs to wait for
the towns fire brigade for assistance, there is not enough time to save protect the project vessel from severe damage.
How can a yard best utilise their resources to reduce their risk?
In general, a yard can define personal responsibilities for each assessed risk, determine the possible remaining exposure and make this information available and transparent. More importantly it should implement emergency plans and conduct regular drills along with having a specific safety concept for each project. Works carried out should be internally quality checked and documented.
For repair shipyards, a way to reduce their overall risk will be to incorporate the ships safety system and crew’s emergency response into the overall emergency response plan.
I know you have your own sailing boat – what would you look for when considering a boatyard for some repair works?
I always look for reference projects of the boatyard, if all the capabilities are inhouse or are carried out with known partners, housekeeping procedures, permit to work, but not for the costs in the first view and finally, knowing that the boatyard covers my vessel only for limited liability I make sure that I have a full insurance on my boat to cover any possible claim.
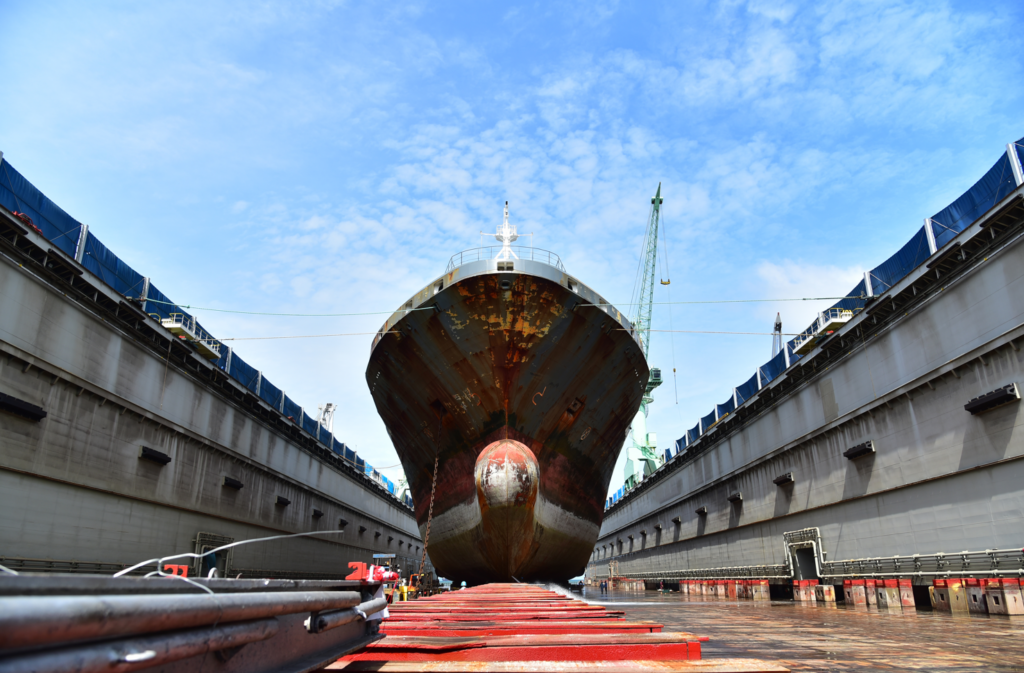
The scope of the JH 143 risk assessment can include, but is not limited to, geographical and environmental risks, general site condition, processes and procedures, quality assurance and quality control of the production process, general housekeeping, management of subcontractors, permit to work systems, emergency response plan, firefighting capability, shipyard equipment, atmospheric monitoring & control of industrial gases, launching & sea trials, site safety and casualty history.
Matthias Wittek is a Naval Architect for ABL, based in Hamburg, with over 30 years of maritime experience. His background includes time as an exclusive class surveyor (GL), maritime administration surveyor, superintendent, hull and machinery damage surveyor and maritime warranty surveyor. He has assisted in the creation of the JH143 risk assessment standard and has been doing this type of surveys ever since.
ABL’s legacy is rooted in the investigation of maritime incidents, dating back to 1856, to the origins of marine surveying with The Salvage Association. Its founding motto – Quaerite Verita – to seek the truth as an independent 3rd-party inspector or consultant, to investigate and report on all aspects of marine incidents, still lies at the foundation of our business today.
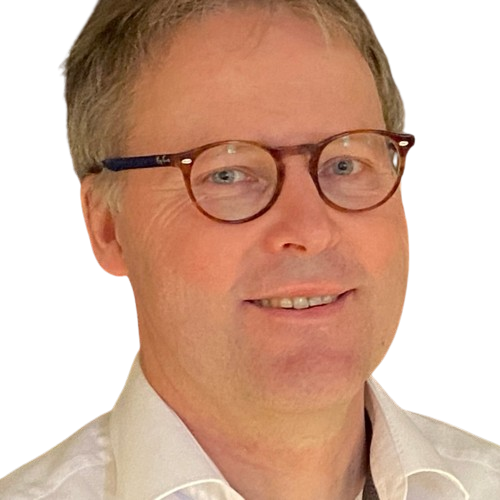
Matthias Wittek
Naval Architect for ABL