How automated asset tracking and workflows can benefit Logistics Managers
Logistics Managers can significantly reduce risks and unlock major efficiencies by deploying automated asset tracking and workflows across key equipment.
Having instant access to accurate, reliable information provided by digital tracking technologies (RFID, NFC, QR codes, and barcodes) can help you to protect the value of your plant or company, identify cost and resource saving opportunities, and minimise risk.
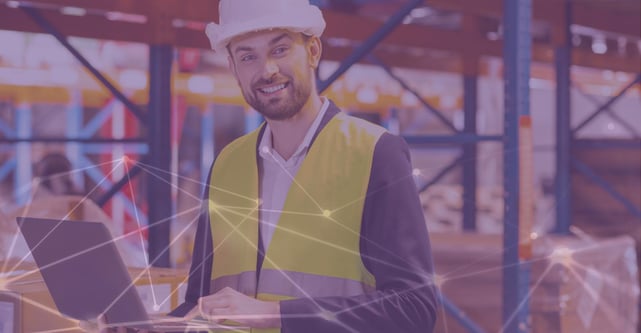
Using digital tracking technologies gives your equipment a digital identity, and allows you to associate detailed information with that identity – such as where it’s been, its current location, its service history, its cost, its maintenance, and much more – so that strategic decisions can be made with confidence.
In this blog post, we explore the key benefits automated asset tracking can bring to Logistics Managers…
What equipment is digital tracking useful for?
Digital tracking is extremely useful for equipment that ticks the following boxes:
- It moves around a lot, or has complex movements
- There are lots of that equipment type, or subtle variations that need to be known
- The consequences of something going wrong with that piece of equipment are high
- It is of high value
Often, it’s not just a case of maintaining equipment – many key pieces will have to be rotated or changed out, and challenges can arise when equipment starts to move about. If you have an RFID tag on mobile equipment, you can track it’s every movement and ensure you can locate it and gain access to its associated information (such as certification, data sheets, etc), when you need it.
RFID tagging is also helpful when you have many variations of an equipment type, for example installing RFID tags may be beneficial for some companies with a large number of detectors with subtle differences. Having a unique tag will allow you to differentiate between them very easily, and avoid any issues or confusion.
How automated tracking can help with temporary equipment
In addition to the equipment categories discussed above, automated tracking can be incredibly useful when it comes to temporary equipment – where effective management of this type of equipment can be challenging and thus expensive.
Most plants or companies have a whole host of temporary equipment being hired from vendors as part of a campaign or project – ranging from generators, and ancillary equipment to hoses and lifting equipment. This is often a grey area, as temporary equipment can be difficult to keep track of and can often be forgotten about. In some cases, temporary equipment can get stuck in a store facility because nobody knows who it’s being rented from.
By adding unique tags to temporary equipment when it arrives on your plant or to your company, you and your team will know who owns it, where it is at all times, and all of its associated information which is key for efficient management of change. This is even more critical for perishable equipment, for example, pipes you need to monitor – as these would not be included in your fixed asset register.
Save costs and time:
At the highest level, digital tagging can ultimately help you protect the value of your plant or company, and avoid significant or unexpected losses. However, there are several key tangible efficiencies that can be unlocked:
- Operations, particularly turnarounds, are much more efficient, and you have a higher level of assurance that everything is as it should be.
- Having a unique identifier prevents equipment from being lost. Warehouses can lose track of equipment quickly because of their fast-paced environment, so this is extremely helpful and will help reduce losses or wasted costs by replacing equipment that is already on the plant or site.
- With temporary equipment, you are usually charged a rental fee on a monthly basis. If the equipment is lost, or the vendor is unknown, these fees will continue unnecessarily. Using digital tagging will not only ensure you know the location and vendor of the piece of equipment, but you’ll also be able to set up notifications associated with the RFID tag to remind your team when the hire is up for renewal.
- The entire team will become more efficient, as they’ll have access to a shared source of accurate, up-to-date information. It is commonplace for only a select number of people to have access to certain information, but this removes the reliance on individuals as information and data is available to the entire team.
- Manual updating and maintenance of spreadsheets or notepads will no longer be required, and there will be more consistency in the information associated with equipment. This will minimise time wastage and issues caused by human error.
Minimise risk and assure safety:
To effectively minimise risk and ensure safe, efficient operations, automated asset tracking can be extremely helpful. If you have a piece of kit, but you don’t know where it is or what it is, what are the risks associated with that? What if something needs to be maintained, or something is in the incorrect place?
Automated tagging gives you absolute assurance that you know what is on your asset, that your equipment is in the correct place, and that the team has all of the important information about that equipment to make informed decisions to mitigate risk, and assure safety.
Introducing AssetVoice™: automated asset tracking and management of change software
We have developed a unique solution to provide Logistic Managers with automated and real-time asset tracking, that cuts costs and maximises productivity.
This award-winning automated change management software, utilises digital tracking technologies and sensors to monitor, track, and manage mobile and critical assets in the most effective and efficient way possible.