5 best practices of effective materials management
Materials management can be described as the process of planning, organising and controlling the flow of materials, from the initial purchasing of raw materials to the final point of delivery – and everything in between.
Managing materials effectively ensures that any company dealing with the movement and supply of materials has the relevant stock and inventory needed to continue production, eliminating the risk of stock shortages or overstocking. The key to effective materials management is adopting best practices that streamline the processes, help reduce costs and improve productivity.
In this blog post, we discuss the top five best practices of effective materials management that businesses can adopt to optimise their operations and help take their materials management programme to the next level…
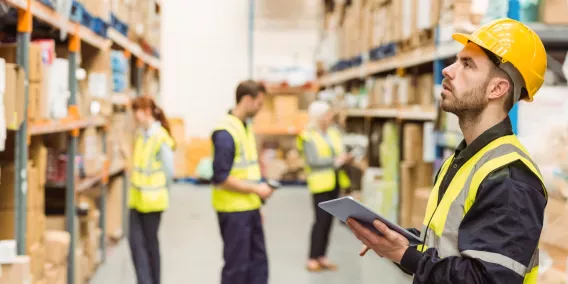
1. Optimise your inventory management
Effective inventory management is crucial for businesses to ensure they have enough stock on hand to meet operational demand without holding excess inventory. Surplus stock is one of the biggest challenges faced by materials management teams, as it ties up capital and creates expensive storage costs.
To manage inventory efficiently, setting up a robust tracking system that monitors stock movement and provides real-time visibility into inventory levels is a recommended solution to overstocking. Materials management teams should also conduct regular audits to reconcile physical inventory with the inventory tracking system to ensure accurate inventory levels.
Another best practice when it comes to inventory management is identifying criticality to determine which inventory is most important to keep close to hand based on how critical it is to production and safety if your asset or equipment were to fail.
By implementing these strategies, businesses can optimise their inventory management, reduce costs, and maximise production.
2. Utilise advanced technologies
Technology is growing at a rapid pace and with the emergence of industry 4.0, it is now simply no longer an option for companies to remain competitive without leveraging new technologies. As a result, it is imperative that companies utilise intelligent ways of operating, no matter which industry they operate in.
There are now lots of technological solutions available on the market designed to help materials managers and manufacturers improve their processes and unlock efficiencies. For example, barcoding, IoT devices and warehouse management systems have been created to carefully manage and track inventory.
At Add Energy, we have designed a myriad of world-class digital software solutions designed to increase the visibility and traceability of materials and assets, including AssetVoice.
We understand that it can sometimes be difficult to achieve materials management excellence, which is why we recommended that industries take advantage of the power of digital technologies. Don’t be afraid of the move towards digitalisation, embrace it as a best practice!
3. Ensure accurate data analysis and forecasting
Data analysis and forecasting play a large role in materials management and should be conducted regularly as a best practice. Leveraging the power of accurate data helps to provide valuable insights that aid decision-making in areas such as procurement, inventory control, production planning and scheduling.
Accurate data and forecasting can also highlight key trends and patterns in material usage while identifying areas of inefficiency, giving material managers the opportunity to improve and manage materials more efficiently.
For instance, our team was contracted by a client to help validate, enrich and build the equipment Bill of Materials (BoMs) to ensure maintenance, supply chain and materials teams had access to the correct data. The work conducted by our team during this project helped to save the client in excess of 16 million dollars per year on supply chain costs, maintenance work planning and execution efficiency gains.
By analysing historical data and applying forecasting techniques, materials management teams can:
- Better anticipate the future demand for their assets, helping to plan for predicted inventory levels and avoid the chance of stock-outs or overstocking.
- Enhances productivity both within the team’s processes and procedures, as well as overall facility output, which is why it is crucial to be considered as a best practice in achieving excellence in materials management.
- Reduce your company’s carbon footprint as you will have implemented forecasting techniques from analysing robust historical data thus enabling you to procure materials in a more efficient manner, potentially by setting up contracts with local vendors at a more competitive price as you have a better foresight of your future demand.
4. Prioritise quality control
Quality control is another essential best practice of effective materials management as it helps to ensure that the materials sourced meet the required standards. When quality control is neglected, companies could end up using poor quality materials in their equipment and assets, which can result in costly breakdowns and equipment failures. Moreover, this can cost companies significant amounts of money in lost production and immediate repairs.
Failing to prioritise quality control could have even more significant implications as well, such as an increase in incidents and accidents, potential environmental harm, and damage to the overall reputation of the company, leading to further loss in sales and revenue.
By implementing stringent quality control procedures as best practice, these issues and potential losses can be minimised by identifying and monitoring the quality of materials consistently, and preventing problems further down the line.
5. Implement a consistent process across your team
Implementing a culture of consistency can bring many benefits to materials management teams as it leaves less room for error when it comes to dealing with materials, particularly spare parts management. For example, consistent processes allow for a smoother and more streamlined workflow, reducing the chances of mistakes being made and making it easier for materials managers to train new staff.
If processes are inconsistent and not shared amongst the whole team, then often room is left for confusion and finger-pointing when mistakes are made. Subsequently, when it comes to achieving an effective materials management program, the best practice is to ensure that your whole materials team is equipped with the same knowledge and training in materials management processes.